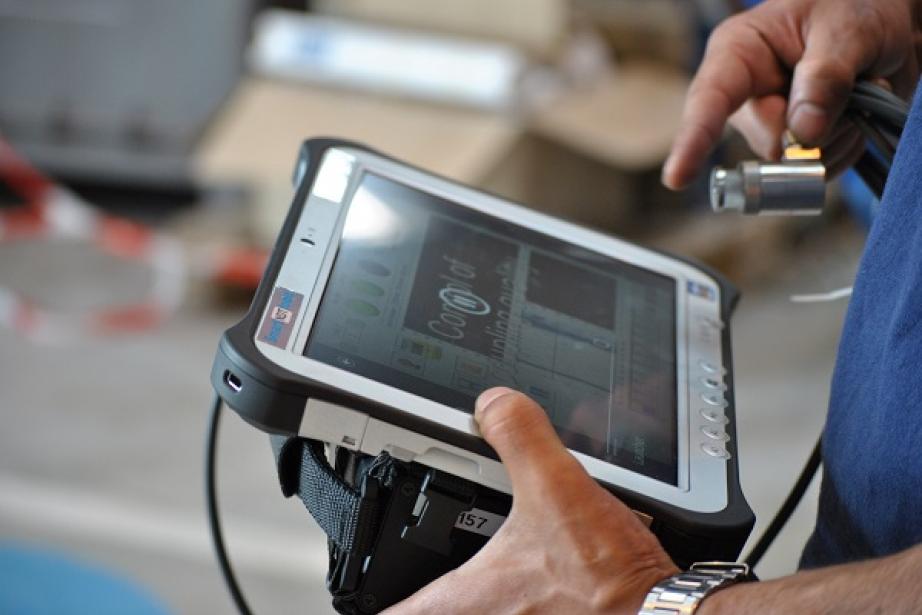
Les outils digitaux de Testia optimisent les opérations de contrôle.
« Le joyau de Testia, ce sera demain ses produits et équipements. Je pense que c’est en grande partie cette activité qui va porter notre croissance », prévoit David Rottembourg, à la tête de Testia depuis près de deux ans. L’Airbusien est passé par la production, le contrôle qualité, l (...)
La suite est réservée aux abonnés
Abonnez vous au magazine
Entreprises Occitanie et accédez à
tous les contenus du site en
illimité.
- 10 numéros/an d’Entreprises Occitanie
(valeur 67 €) - Le hors-série Top Economique Occitanie
offert - L'intégralité des articles sur le site
Déjà inscrit ? Connectez-vous